Cliff and Ian recently visited Kebur’s porcelain suppliers in Italy and Spain to check out the manufacturing process, the product ranges and to strengthen our partnerships.
In Italy most of the many producers are based in or near the Sassuolo area, just south of Modena in the province of Emilia-Romagna. In Spain it’s very similar with a high concentration of factories in the Castellon area just north of Valencia.
Whilst there are many tile producers, a relatively small proportion currently produce the 20mm thick tiles suitable for exterior paving.
In all the factories we visited, the manufacturing process is very similar. Technicians scan real wood, stone or concrete pieces that they want to recreate as porcelain tiles. The scanned images are then manipulated or “photoshopped” to produce a series of designs for the tiles.
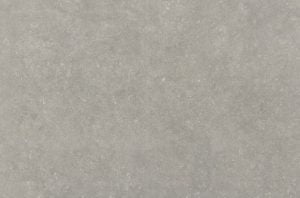
Contempo Gris Royale Porcelain Paving is formed from scanning real limestone
The carefully selected raw materials of clay, sand and other minerals are mixed and stored in silos. Different colours are produced to form the appropriate coloured bodies for each specific type of tile. The silos then feed large presses that press the tiles in molds at around 600kg per cm².
At this stage the formed tile is solid but can be snapped like a biscuit.
The tiles are then dried to remove the moisture, before moving on to a conveyor system where a glaze is applied and then digitally printed, with the ink penetrating through into the top layers of the paving. This relatively new digital printing technology has hugely improved the quality of the final appearance of the tiles in recent years.
Robots transport the tiles in giant racks from one stage to the next.
The tiles are now ready for the kiln. They enter a kiln that is around 100-130 metres long at around 400°C and pass through the kiln on rollers. In the middle of the kiln the temperature reaches around 1220°C before cooling down again towards the end. The 20mm thick tiles are in the kiln for around 1hr 10 mins to 1hr 30mins.
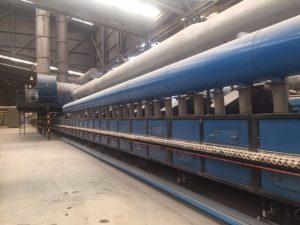
Kilns are 100-130 metres long
Supervisors are checking for quality at every stage of the process, but after cooking the tiles are scanned by a computer as well as human eye to detect any defects.
If the tiles are going to be rectified (cut to dimensionally accurate size) like Kebur’s are, they go through saws/grinders and are then sorted and packaged up with batch and tone codes ready for dispatch.
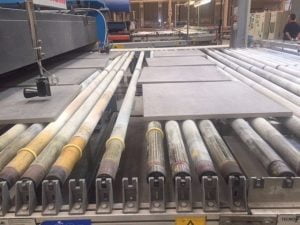
Cooked tiles emerge from the kiln
The post Porcelain Paving Production: An Overview appeared first on Kebur.